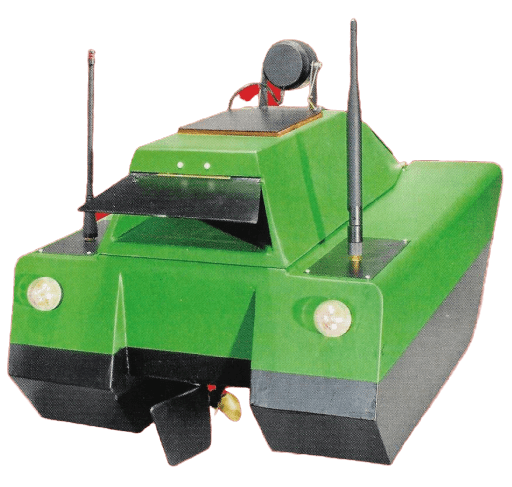
La première partie de cet article concernait la construction de la coque et de la cabine. En espérant que de nombreux lecteurs ont été intéressés par ce sujet, nous décrivons aujourd’hui la motorisation, la finition, les servomoteurs et la caméra
Nous aborderons ensuite la partie électronique avec la télécommande
conçue pour ce bateau, télécommande simple où la partie RF a été réduite à sa plus simple expression par l’emploi de modules émetteurs/récepteurs performants
Le choix de la motorisation d’un modèle réduit est une des choses les plus importantes dans la construction de celui-ci.
Puisque nous disposons de deux batteries de 12 V / 7 A.h, dont l’une est réservée à l’alimentation du moteur et que nous ne pouvons aller au-delà de cette capacité pour des raisons de place et de poids, nous ne pourrons utiliser un moteur consommant plus de 2,5 A, l’autonomie ne serait alors pas suffisante.
Nous aurions pu envisager l’utilisation de batteries CdNi ou NiMH, moins lourdes, mais le prix des packs de capacité élevée est prohibitif: plus du double à capacité égale.
Un seul moteur répond, à peu de choses près, à ce que nous recherchons : c’est le moteur Mabushi RS540/1 dont les caractéristiques sont données ci-après.
Motoréducteur MFA type 91902.51 (tension d’alimentation comprise entre 4,5 V et 15 V, tension nomina¬le de 12 V) :
Caractéristiques du moteur sous 6V:
A vide, vitesse de 7500 tlmn, courant de 0,45 A
En charge, vitesse de 6180 tlmn, courant de 2,1 A
Couple moteur de 1,182 N/cm Puissance de 7,49 W Efficacité de 59,4 %
Caractéristiques du moteur sous 12 V:
A vide, vitesse de 15800 tlmn, courant de 0,52 A
En charge, vitesse de 13360 tlmn, courant de 2,85 A
Couple moteur de 1,544 N/cm Puissance de 21,2 W Efficacité de 61,9%
Caractéristiques physiques du motoréducteur MFA type 91902.51 avec boîte de réduction 2,5 :1 :
Longueur de 80 mm Diamètre de 39 mm
Longueur de l’arbre de 15 mm Diamètre de l’arbre de 6 mm Poids de 240 g
Couple de 2 kg/cm (et 6 kg/cm en durée courte)
Vitesse du motoréducteur MFA type 91902.51 avec boîte de réduc¬tion 2,5:1 :
Avec 4,5 V : 2250 tlmn Avec 6 V : 3000 tlmn Avec 9 V : 4500 tlmn Avec 12 V : 6300 tlmn Avec 15 V : 7900 tlmn
De plus, le motoréducteur MFA type 540 est livré sur un support. Il ne reste plus qu’à le visser dans la cale du bateau, ce qui n’est pas le cas avec les autres moteurs.
Pour que le moteur soit pratiquement dans l’alignement de l’axe de l’hélice,
il est nécessaire de le monter sur une planchette de contreplaqué de 3 mm d’épaisseur, collée contre la coque du bateau selon un plan incliné (photo E). Utiliser le dessin A de la planche 9 pour le relevé des cotes. Quatre vis de 3 mm sont fixées sur cette planchette de contreplaqué. Les positions sont déterminées par les trous existants dans le support du moteur. Les vis sont tout d’abord fixées seules, au moyen de rondelles et d’écrous. Les têtes sont ensuite noyées dans de la colle « époxy».
Visser ensuite deux écrous sur chaque vis, de manière à pouvoir monter ou descendre légèrement le moteur afin d’obtenir un alignement parfait entre l’axe de celui-ci et l’axe de l’hélice. Une rotation sans points durs, comme celle représentée par le dessin B de la planche 9 doit être obtenue. Le tube d’étambot (planche 10) est un modèle de 170 mm de référence 002321 (fournisseurs en fin d’article). Lorsqu’il sera mis en place dans le bateau, celui-ci sera rempli de graisse de bonne qualité.
Afin de le mettre en place, couper d’abord la partie de diamètre 3 mm. Au moyen d’un forêt de 06 mm, pratiquer un trou oblong dans la coque. Fixer provisoirement le moteur équipé du cardan « deux pièces» sur son support puis fixer l’axe d’hélice à l’autre partie du cardan. Monter l’hélice dont l’extrémité de l’une des pâles positionnée en haut et perpendiculairement à la coque devra se situer au minimum à 18 mm du trou de passage du gouvernail.
Avant de coller le tube d’étambot, ce dernier étant positionné à sa place définitive, on tournera l’hélice de manière à s’assurer qu’il n’existe pas de points durs (vous pourrez de toute façon positionner exactement le moteur plus tard). Mettre ensuite de la colle « époxy» autour du tube, à l’endroit de son passage dans la coque et le maintenir jusqu’à ce qu’elle « prenne ».
Cela fait, coller autour du trou du tube d’étambot, des baguettes de section carrée de 5 mm. La petite cuvette ainsi réalisée est ensuite remplie jusqu’en haut de colle « époxy» qui, après durcissement, maintiendra fermement le tube (planche 11).
Tracer et découper la pièce de bois qui sera collée à l’extérieur de la coque, entre cette dernière et le tube.
L’hélice, comme le moteur, sont les points les plus importants pour la propulsion du bateau. Cela semble être une lapalissade, mais le choix d’une hélice n’est pas aussi simple qu’il y parait au premier abord.
Pour notre part, nous nous sommes basés sur le fait qu’il est préférable d’utiliser une hélice à grand pas et diamètre important entraînée par un moteur tournant plus lentement, plu¬tôt qu’une hélice de faible diamètre et à petit pas couplée à un moteur extrêmement rapide.
Nous avons choisi une hélice de bonne qualité de marque Rivabo, en laiton, de référence 120534061. Ses pâles sont soudées à l’argent. Elle est d’un diamètre de 60 mm et d’un pas de 61 ,5 mm. Elle est prévue pour une vitesse de rotation de 5800 tlmn maximum, ce qui est à peu de choses près la vitesse de rotation de notre moteur en charge.
Avec cette hélice, il faut reconnaître que notre bateau avance à bonne allure, peut-être même un peu trop rapidement. Vous pourrez alors faire des essais avec une hélice de 50 mm ou même 45 mm. Sinon, vous pour¬rez choisir un moteur tournant moins vite (le MFA type 919D61 présente une vitesse de rotation de 2633 tlmn et un couple de 3 kg/cm, 9 kg/cm en durée courte) et garder la même hélice de 60 mm.
Pour information, le pas d’une hélice indique théoriquement, la distance que parcourt le bateau propulsé, pour un tour de cette hélice. C’est une indication théorique, car un facteur important entre en jeu : le glissement, qui réduit le rendement de 35 % à 40 %.
La construction achevée, vous pourrez passer à l’étape de la finition. Toutes les aspérités ayant été éliminées à la lime et les angles ayant été arrondis, l’ensemble du bateau sera passé au papier de verre assez fin, afin de le débarrasser des dernières échardes et traces de colle.
Nous allons pouvoir entreprendre la pose de l’enduit. Pour notre part, nous utilisons du mastic « polyester» réservé à la carrosserie automobile (de marque Sintofer ou autre) pour les épaisseurs importantes.
Vous pouvez facilement vous en pro-curer dans les grandes surfaces ou chez les revendeurs de matériel automobile. Il présente l’avantage de sécher rapidement (quelques minutes) en fonction de la dose de catalyseur qui lui est adjoint.
Il ne faut donc pas en préparer des grandes quantités à l’avance. D’autre part, il convient d’enlever l’excédent déposé sur le bois avant qu’il ne durcisse complètement, car il devient alors très dur et difficile à poncer.
Arrondir d’abord les angles intérieurs entre la coque centrale et les flotteurs, y compris le panneau arrière, puis entre les baguettes de section carrée de 5 mm et le pont (planche 3, vue de devant) en y plaçant de l’en¬duit à l’aide d’un doigt. Exécuter la même opération pour la pièce triangulaire soutenant l’axe d’hélice. Boucher ensuite tous les petits trous existants. Passer une fine couche de mastic de finition sur tout le bateau, puis la poncer.
Recommencer cette opération jusqu’à obtenir une surface absolument lisse, sans trous ni bosses.
Pour la mise en peinture, choisir bien entendu une peinture « glycero », sati-née, de préférence en bombe, afin d’obtenir un meilleur résultat. Deux ou trois couches sont nécessaires. Pour ce qui est des couleurs, celles-ci étant une affaire de goût, chacun choisira.
I! sera tout de même nécessaire de tracer la ligne de flottaison, soit en choisissant deux couleurs différentes de part et d’autre de la coque, soit en la traçant d’une autre couleur.
Les dessins de la planche 11 donnent une indication sur les positionnements, dans le bateau, des servomoteurs et des accessoires. Nous ne donnons qu’une indication approximative de l’implantation des servomoteurs, sans cotes, car leurs emplacements se feront en fonction de leurs tailles.
Nous avons placé le projecteur sur la cabine. Celui-ci a été fabriqué à partir d’une petite « lampe torche » de poche à six leds. Nous avons gardé la partie réflectrice que nous avons travaillée à notre goût.
Nous avons également équipé le bateau de feux de positionnement : deux rouges à l’arrière. Cela s’avère très utile lors des pêches de nuit. Ces feux utilisent des diodes leds « haute luminosité » en boîtier cristal de diamètre 05 mm. Chacun réalise¬ra l’habillage à son goût.
Les deux batteries de 12 V /7 Ah sont situées, chacune, dans un caisson. Elles seront mises en place avant l’installation des servomoteurs et de la télécommande. Leurs positions définitives dans les caissons seront déterminées lors de la mise à l’eau du bateau. Les batteries seront plus ou moins amenées vers l’avant ou vers l’arrière afin de mettre le robot bateau « de niveau ».
Pour indication, dans notre robot bateau, si le centre des batteries est placé au niveau des entretoises centrales, le robot bateau est équilibré.
Nous avons pensé qu’il serait très attrayant d’utiliser une caméra pouvant montrer, sur un moniteur, des images émise depuis le robot bateau, aussi bien du paysage que sous l’eau. Cette fonction ne se rencontre que sur les robots bateaux amorceurs « haut de gamme» du commerce.
Cette option grève le prix de revient de notre réalisation d’environ 150,00 €, mais elle reste facultative et chacun fera en fonction de son budget.
Nous avons utilisé une caméra cou¬leur de petites dimensions: longueur environ 60 mm sur un diamètre de 52 mm. Elle est prévue pour fonctionner en extérieur. Nous voulons pouvoir réaliser des prises de vues sous l’eau, à trois ou quatre centimètres de la surface. Elle ne sera donc pas soumise à une pression importante. Bien que ses ouvertures soient munies de joints d’étanchéité, il suffit, avant fermeture, de déposer un joint de colle silicone (colle pour verres d’aquarium). Faire de même autour du verre protégeant l’objectif. La caméra est ainsi rendue étanche.
Le modèle utilisé est équipé de leds » infrarouge », ce qui permet une vision nocturne sans aucune lumière. Pour ce qui est de l’installation, se référer aux dessins donnés sur la planche 12. La caméra est fixée au moyen d’un tube en laiton coulissant sur deux axes. Ces deux axes sont constitués de deux barres en laiton, elles-mêmes fixées sur chacun des flancs internes du bateau au moyen de deux flasques. Les deux supports, en époxy cuivré « double faces » sont soudés sur le tube en laiton et vissés sur la caméra.
Un palonnier, fixé sur le tube en laiton et relié à un servomoteur, permet le basculement de la caméra, de sa position horizontale à une position verticale, pour la prise de vues sous-marine. Nous voici parvenus au terme de la réalisation du robot bateau.
Nous espérons qu’elle a répondu à vos attentes.
Pour donner vie à notre maquette « flottante « , voyons maintenant la partie électronique qui va la téléguider.
La mise au point de montages HF étant toujours délicate, nous avons basé la conception de notre télécommande sur l’emploi de modules RF intégrés. Ainsi, le fonctionnement est assuré, sans réglages, dès la mise sous tension. Nous avons choisi le modem TDL2A-433-9 de Radiométrix, distribué par la société Lextronic, modem que nous avons utilisé à maintes reprises sans jamais avoir rencontré le moindre problème. Son schéma interne est donné en figure 1, tandis que la figure 2 représente ses caractéristiques physiques.
Les principales caractéristiques du TDL2A-433-9 sont les suivantes :
– Fréquences de travail sur cinq
canaux:
433,925 MHz, canal 0 (par défaut) 433,285 MHz, canal 1
433,605 MHz, canal 2
434,245 MHz, canal 3
434,465 MHz, canal 4
– Stabilité en fréquence de ± 10kHz
– Largeur de canal de 320 kHz
– Alimentation en +5 V
– Consommation de 22 mA en « réception » et 28 mA en « émission »
– Puissance d’émission de 10 dBm (10 mW)
– Sensibilité du récepteur de -107 dBm
– Réjection de la fréquence « image»
de -50 dBm
– Interface:
9600 bps, half duplex
1 bit de start, 8 bits de données,
1 bit de stop, pas de parité Butter de 32 octets
8 adresses
Dans notre cas, il est nécessaire que plusieurs modems puissent fonctionner en même temps dans le même périmètre et qu’aucune interférence ne vienne brouiller les ordres émis. Le microprocesseur interne permet le paramétrage du modem : sa fréquence d’émission et l’adresse.
Trois des broches du modem sont utilisées pour sa programmation :
– La broche 16, ENABLE est active au niveau « bas ». Une résistance interne de 47 kQ la connecte au +Vcc. Elle doit être portée au niveau « bas », afin de valider le fonctionnement du module – La broche 15, SETUP, est connectée à la masse lorsque l’on veut entrer dans le mode de programmation du module. Une résistance de tirage de 47 kΩ la connecte au +Vcc
– La broche 11, STATUS, présente un niveau « haut » lorsque des données valides arrivent dans le buffer de réception. Ce signal permet de signaler au microcontrôleur l’arrivée d’un packet. D’autre part, cette broche, connectée à une diode led indicatrice, permet des vérifications de portée entre les deux modems Afin d’entrer dans le mode de programmation, la broche SETUP est reliée à la masse, ce qui désactive la partie radiofréquence. Il suffit ensuite d’envoyer les ordres au module au moyen de la connexion » série », Trois commandes principales existent:
– ADDRO à ADDR7 : cette commande permet de choisir une adresse de travail parmi huit. C’est avec ce paramètre que nous configurerons notre télécommande, ce qui permettra la cohabitation de huit bateaux sur le même site
– CHANO à CHAN4 : cette commande permet de sélectionner la fréquence d’émission. Un modem ne peut communiquer avec un autre modem que si l’adresse et le canal sont identiques pour les deux unités. Les numéros « d’adresse» et de « canal» sont stockés, une fois programmés, dans une mémoire volatile qui s’effacera à la coupure de l’alimentation. A la mise sous tension, ce sont les valeurs programmées dans la mémoire EEPROM qui seront, par défaut, les valeurs de travail. Donc, si vous souhaitez modifier ces valeurs par défaut, il conviendra d’utiliser l’instruction suivante:
– SETPROGRAM : cette commande écrit, dans la mémoire EEPROM, l’adresse et le canal que l’on vient de programmer et qui deviennent les nouvelles valeurs par défaut. Le caractère « – » (ASCII 126 décimal) est envoyé par le module et signale au terminal la fin du cycle d’écriture en mémoire EEPROM.
Trois autres commandes sont disponibles. Elles permettent d’éventuels réglages et tests :
– NOTONE : transmet une porteuse non modulée
– LFTONE : transmet une porteuse modulée par un signal carré d’une fréquence de 8 kHz
– HFTONE : transmet une porteuse modulée par un signal carré d’une fréquence de 16 kHz
– # : stoppe l’émission. Ce caractère (CR = Carriage Return, retour chariot) doit être envoyé après chaque commande afin que celle-ci soit prise en compte.
Le schéma de principe de la partie « émetteur» de notre télécommande est donné en figure 3.
L’utilisation d’un microcontrôleur simplifie la conception de l’émetteur. En effet, dans une télécommande classique, c’est un train d’impulsions de durées variables qui est envoyé au récepteur afin de modifier la position des servomoteurs.
Ici, c’est une suite de données « série» qui est générée et transmise.
Ces données indiquent la position des potentiomètres et des boutons poussoirs au microcontrôleur du récepteur, Il positionne en conséquence les servomoteurs et alimente ou non les relais électromécaniques. Nous avons prévu la possibilité d’utiliser six voies « proportionnelles » et six voies «tout ou rien» :
– Voie 1 : servomoteur de direction
– Voie 2 servomoteur d’arrêt/marche, avant/arrière et vitesse – Voie 3 : servomoteur d’orientation de la caméra
– Voie 4 : servomoteur d’orientation du projecteur
– Voie 5 : servomoteur d’ouverture/ fermeture de la trappe de largage
– Voie 6 : utilisation « optionnelle » du sixième servomoteur
Le récepteur utilise des relais bis-tables. Deux voies sont donc nécessaires à la commande d’un relais.
– Voies 7 et 8 : mise sous tension et hors tension de la caméra
– Voies 9 et 10 : allumage/extinction des diodes infrarouges de la caméra – Voies 11 et 12 : allumage/extinction des feux de position et du projecteur
Les curseurs des potentiomètres R3 à RB, connectés entre +DZ et masse, délivrent une tension proportionnelle à leurs positions aux entrées ADCO à ADC5 du convertisseur AlD interne au CB220. La tension OZ, très stable, puis qu’issue d’une diode zéner de référence, peut être ajustée entre +5 V et + 10 V. Nous avons choisi cette option afin de pouvoir réduire, le cas échéant, la course des potentiomètres. Certains trouveront en effet fastidieux de devoir manœuvrer les manches sur 270°. En augmentant la tension de référence, la course diminuera d’autant. Cependant, il conviendra d’être très prudent lors du réglage de cette tension, le convertisseur n’acceptant pas des tensions supérieures à +5 V. Des butées devront obligatoirement être mises en place sur les axes des potentiomètres afin d’en limiter la course.
Les commutateurs S2 à S7, connectés aux lignes P8, P9, P12, P13,_ P14 et P15, permettent de leur appliquer un niveau « haut », Ces commutateurs commandent le positionnement des relais du récepteur.
Les commutateurs S9, S10 et S11 déterminent sur quelle adresse fonctionnera le couple d’émetteur / récepteur. Les diodes LED8 à LED10 visualisent le positionnement de ces commutateurs. Il faut remarquer que ce paramétrage doit être effectué avant la mise sous tension de l’émetteur. Si la position des commutateurs est modifiée durant le fonctionnement, un RESET devra être effectué au moyen du bouton poussoir S8.
Le microcontrôleur CB220 communique avec le modem, au moyen de ses lignes RX et TX, respectivement les ports P10 et P11 , La ligne P7 permet de positionner le TDL2A-433-9 soit en « émission/réception -. soit en mode « programmation » (SETUP). La diode LED11 signale ce dernier mode par son extinction. La diode LED12 signale, par de brèves illuminations, la réception des signaux d’acquittement émanant du récepteur.
Les deux tensions 5 V et 12 V nécessaires au fonctionnement de la platine sont fournies par des convertisseurs, Le LT1300 est configuré en convertisseur « abaisseur/élévateur » et génère le +5 V. Il peut débiter un courant de 200 mA. Le MAX732, « convertisseur élévateur « , fournit le + 12 V nécessaire à la diode zéner de référence, la TL431 CLP.
Un filtre passe-bas placé en sortie et constitué de L4 et C14 permet d’obtenir une tension très « propre ». Seulement quatre accumulateurs d’une capacité de 2000 mAh sont nécessaires au fonctionnement de l’émetteur et procurent une autonomie plus que suffisante. Un connecteur et une diode permettent le raccordement d’un chargeur.
Deux circuits imprimés sont nécessaires à la réalisation de l’émetteur: le premier supporte l’émetteur proprement dit, tandis que le second, de mêmes dimensions, permet la fixation des potentiomètres et des divers commutateurs.
Le dessin du circuit imprimé de l’émetteur est donné en figure 4, la figure 5 et la photo F donnant le schéma de l’implantation des composants. La figure 6 représente le dessin du circuit imprimé de la platine secondaire, tandis que la figure 7 en donne le schéma d’implantation. Le câblage de la platine de l’émetteur doit être réalisé en respectant l’ordre suivant:
1/ souder tous les straps, puis les résistances. Les résistances R9, R11, R12, R15″ R17 et R19 peuvent être remplacées par un réseau de huit résistances dont seulement six seront utilisées Sinon, on se reportera au schéma donné en figure 8 pour le soudage des résistances individuelles
2/ implanter tous les condensateurs, non chimiques, puis les supports des circuits intégrés
3/ placer les diodes, la diode zéner de référence et le transistor
4/ souder les quatre inductances, le bouton poussoir de RESET et les condensateurs chimiques
5/ souder le connecteur de « charge» et le connecteur d’antenne
6/ souder enfin les commutateurs S9, S10 et S11 qui sont des morceaux de « barrette » sécable de picots sur lesquels sont placés des cavaliers
7/ les diodes leds sont à souder « côté cuivre », en laissant des longueurs de broches suffisantes pour qu>elles se logent dans les trous pratiqués dans la platine secondaire (photo G)
En ce qui concerne le câblage de cette dernière, peu de composants sont à implanter. Sur le schéma de la figure 3, l’encadré en ligne pointillée de couleur rouge indique ceux qui sont à souder. La connexion entre les potentiomètres, les commutateurs et la platine se réalise au moyen de fils de câblage du « côté cuivre » (photo G).
La jonction entre la platine « émetteur » et la platine « secondaire » est réalisée de la manière suivante: souder, « côté cuivre », des morceaux de supports « tulipe ». un à six points et un à deux points pour les potentiomètres, un à six points et un autre à un point pour les commutateurs et ce, sur les deux platines. Il suffira ensuite d’insérer des morceaux de fil de câblage rigide, d’un diamètre suffisant, dans les supports, afin d’interconnecter les deux platines. Quatre entretoises fixeront les deux circuits entre eux.
ÉMETTEUR
• Résistances
R1, R10, R13, R14, R16, R18,R20, R35 : 470 Ω (jaune, violet, marron)
R2 : ajustable multitours 10 kΩ
R3, R4, R5, R6, R7, R8 : potentiomètre linéaire 10 kΩ
R9, R11, R12, R15, R17, R19, R32, R33, R34 : 10 kΩ (marron, noir, orange)
R21, R22,R23, R24, R25, R26, R28, R29, R30, R31, R36 : 1 kΩ (marron, noir, rouge)
R27 : 560 Ω (vert, bleu, marron)
• Condensateurs
C1 : 47µF / 25 V
C2,C5,C6,C7,C8,C9,C10,C13,C15, C16, C18, C24: 100 µF
C3, C11, C12, C14, C23: 100 j.JF / 25 V tantale
C4, C25 : 10 µF / 25 V
C17 : 10 nF
C19: 2,2 nF
C20: 150 nF
C21 : 330 j.JF / 25 V
C22 : 22 j.JF / 25 V
• Semiconducteurs
LED1 à LED7, LED11 : diode électrolu-minescente, rouge, haute luminosité
LED8, LED9, LED10 : diode électroluminescente, jaune, haute luminosité LED12 : diode électroluminescente, blanche, haute luminosité
02,03: 1N5817
DZ1 : TL431CLP
T1 : BC547
• Inductances
L1, L2 : 27 µH L3: 50 µH
L4: 25 µH
• Circuits intégrés
IC1 : LT1300
IC2 : CUBLOC CB220 (LEXTRONIC) IC3: MAX732
• Divers
1 modem TDL2A-433-9 (LEXTRONIC)
1 bouton poussoir miniature pour circuit imprimé
2 supports pour circuit intégré 8 broches 1 connecteur alimentation
1 connecteur SMA reverse, coudé, pour circuit imprimé
6 boutons poussoirs 1 interrupteur
2 barrettes sécables de supports tulipe (36 points)
Entretoises, vis, rondelles, écrous
Pour la phase des essais, seuls les circuits intégrés LT1300 et MAX732 sont placés dans les supports. Après la mise sous tension, vérifier les tensions en sorties de ces derniers: +5 V pour le LT1300 et +12 V pour le MAX732. Régler ensuite la tension de sortie de la diode zéner de référence au moyen de la résistance ajustable R2 à une valeur de +5 V. Vérifier que la manœuvre des potentiomètres se traduit bien par une variation des tensions appliquées aux entrées du convertisseur du CB220. Constater également que l’appui sur les commutateurs a pour résultat l’illumination des diodes leds et l’application d’un niveau « haut » sur les broches d’entrées du microcontrôleur.
La platine mise hors tension, placer les CB220 et TDL2A-433-9 dans les supports. Les essais complets ne pourront être effectués que lorsque le récepteur sera construit.
P.OGUIC